Mezclado: receta para el éxito
17 December 2020
Las plantas de mezclado se están beneficiando de los avances en todas las áreas de la tecnología, desde iniciativas ecológicas y automatización, hasta el control de calidad y más. En general, se ha demostrado que las plantas actuales están evolucionando hacia una mayor eficiencia en beneficio de los productores y sus clientes.
La tecnología de reciclaje se está volviendo cada vez más importante en todo el mundo, ya que los productores de hormigón y asfalto intentan utilizar los recursos de manera inteligente sin efectos adversos en la calidad de su mezcla.
Según el estudio Demanda y oportunidades del mercado de aditivos de asfalto 2020-2030 de Persistent Market Research, se espera que la creciente demanda de pavimento de asfalto recuperado (RAP) en el desarrollo de infraestructura impulse la demanda de aditivos de asfalto.
El uso de RAP ayuda a reducir el uso de costoso material asfáltico virgen, lo que a su vez ayuda a ahorrar costos en general. Sin embargo, hasta un 30% del RAP debe ser mezclado con asfalto virgen, ya que la adición de un porcentaje más alto de asfalto recuperado podría degradar su desempeño.
Según el mismo estudio, la demanda de asfalto utilizado en la pavimentación de calles y carreteras ha aumentado en los últimos años debido a las mayores inversiones gubernamentales y al crecimiento de las actividades de desarrollo de infraestructura vial.
Para satisfacer la alta demanda de RAP, Ammann, empresa con sede en Suiza, ha desarrollado para el mercado norteamericano, ACP ContiHRT. La planta cuenta con un secador RAP para la adición de materiales reciclados calientes y una alimentación de reciclaje en frío separada que permite desarrollar una mezcla que consta de hasta un 60% de RAP.
“Aquí, las tecnologías de producción de asfalto recuperado se transfirieron de las plantas batch de Ammann a una planta de mezcla continua”, explica Günter Tesch, gerente senior de desarrollo comercial de plantas de Ammann. “Los clientes que prefieren la tecnología de mezcla continua ahora pueden beneficiarse de la experiencia de Ammann y utilizar tecnología probada que establece nuevos estándares”.
“En los últimos años, el enfoque está más alineado con el ahorro de recursos y la reducción de la huella de CO2 a través de medidas como el asfalto a baja temperatura. Esto da como resultado desarrollos en torno a la tecnología de alto RAP, que se vuelve más importante en el mundo de la mezcla actual”, señala.
El secador Ammann RAH100 está diseñado para permitir que una planta mezcladora de asfalto produzca una mezcla que consiste en 100% RAP.
Esencial para el RAH100 es su suave proceso de calentamiento, explica la compañía. Durante el proceso de mezcla tibia, la secadora puede calentar materiales a temperaturas de entre 100ºC y 130ºC. También puede hacer asfalto a 140º-160º si se desea una mezcla más tradicional.
El calentamiento del RAP suele ser el proceso donde surgen las complicaciones. El RAP debe alcanzar su temperatura objetivo, pero el bitumen se dañará si el material se calienta demasiado rápido.
El tambor RAH100 de Ammann fue diseñado para eliminar esa preocupación y consta de dos secciones conectadas. Uno es un generador de gas caliente que contiene un quemador y fuerza el aire hacia la segunda sección, que es un secador de contraflujo.
El RAP entra en el extremo más alejado de la sección del secador de contraflujo y se mueve hacia la cámara de calor. Al final del secador de contraflujo, el RAP se transporta a un silo adjunto. La mezcla calentada sale de la secadora antes de que la temperatura sea excesiva, por lo que nunca alcanza la temperatura crítica en la que se daña el betún.
Eliminando el error humano
En el mundo actual, la automatización extensiva de los procesos de producción es importante para la seguridad de los trabajadores y la calidad del producto. Con menos trabajadores empleados, es clave eliminar el potencial de error humano de la ecuación tanto como sea posible.
Para ayudar con esto, Trimble cuenta con TrimFleet HPS100, un medio automatizado de lectura de la presión hidráulica de la transmisión de la caja de engranajes del tambor, lo que ayuda a los conductores de camiones mezcladoras de concreto a garantizar que llegue una mezcla consistente al lugar de trabajo.
El HPS100 captura los datos en puntos críticos durante el ciclo de entrega con marcas de tiempo y posición para la validación de la calidad. Los despachadores y los operadores de lotes pueden ver lecturas de presión en tiempo real desde sus escritorios sin esperar a que el conductor responda. Los gerentes de control de calidad pueden asegurarse de que el material se mezcle y se vierta correctamente cuando sale de la planta después de agregar el agua monitoreando los datos de presión en TrimView.
“Cuando el hormigón sale de la planta de lotes y entra en el camión, es responsabilidad del conductor tratar de mantener el diseño de la mezcla”, señala JP Schuette, gerente de producto de Trimble Construction Logistics.
La lectura de presión hidráulica indica cuánta presión se necesita para hacer girar el tambor de mezcla cuando está lleno, lo que se correlaciona con el asentamiento. Con esta información, los conductores ya no necesitan ponerse en peligro potencial subiéndose a la parte trasera del camión, y elimina el tiempo dedicado a revisar el material. El HPS100 proporciona una confirmación de que el cliente obtendrá un producto exactamente cómo ha sido solicitado.
“En el panorama más amplio y holístico, realmente se trata de seguridad y calidad y de que las personas obtengan lo que pagaron”, dice Schuette. “Con nuestra aplicación TrimView, el conductor y el despachador pueden ver la lectura. Es realmente útil para el control de calidad”.
Simplificación
Carmix está ayudando a impulsar la industria del hormigón con el desarrollo de tecnologías digitales que simplifican las operaciones en el sitio. Un ejemplo es Concrete-Mate, un sistema de pesaje electrónico que pesa la mezcla de concreto directamente dentro del tambor. En lugar de un sistema de pesaje hidráulico instalado en el cucharón, el sistema Carmix está equipado con cuatro celdas de carga electrónicas en la parte inferior del tambor.
Disponible en el modelo Carmix 3500 TC, este sistema de pesaje permite al operador dosificar y verificar simultáneamente todos los agregados a medida que se cargan dentro del tambor, incluida el agua. Esto simplifica el control de cada agregado, reduciendo el error de dosificación. Además, el sistema puede almacenar hasta 15 diseños de mezcla diferentes con hasta 99 componentes a la vez. Cuando se completa la carga, el PC en el gabinete de control imprime automáticamente un ticket con todos los datos relevantes, que se pueden guardar en una memoria USB.
Concrete-Mate es un administrador de diseño de mezcla digital que ejecuta un software de gestión de nivel de planta RMC que aplica cuatro celdas de carga dentro del conjunto de mezcla para lograr una mezcla de concreto de alta calidad de acuerdo con las normas internacionales de concreto (UNI 206-1 - ASTM - ACI, etc.).
Una vez almacenado el diseño de mezcla deseado, el software sugiere las dosis para cada elemento, la secuencia de operaciones y el tiempo necesario para cada paso del proceso, eliminando así cualquier posible error. Las cuatro células de carga actúan como sensores de peso directamente donde se hace la mezcla.
Concrete-Mate permite controlar la calidad de las operaciones individuales. El software emite al final del proceso un certificado con todos los datos analíticos de Mix-Design.
Asimismo, Carmix ha desarrollado un sistema de monitoreo desde el sitio web (IPOTweb) y desde la aplicación (IPOTAPP) para un monitoreo preciso de la producción y la calidad del producto y los costos de funcionamiento, lo que ayuda a los usuarios a rastrear el retorno de la inversión.
Preocupación en los costos
Existen restricciones presupuestarias en todos los procesos de construcción, especialmente en la era del covid-19, donde los productos básicos son más difíciles de conseguir y, como resultado, cuestan más.
Con ese fin, Liebherr ha introducido la planta mezcladora de hormigón para presupuestos reducidos: la LCM 1.0. El equipo ofrece un montaje rápido y sencillo, con un mínimo de trabajo de cimentación, y produce hasta 60 m³ por hora. Además, se puede transportar en tan solo dos contenedores.
Se encuentran disponibles varios silos de agregados con un volumen de almacenamiento de 40 a 100 m³. La planta puede equiparse con hasta tres silos de cemento (100 toneladas cada uno).
Según Liebherr, la empresa está reaccionando a los requisitos del mercado. La demanda de plantas más pequeñas, optimizadas para el transporte y con un presupuesto manejable está creciendo a medida que más y más contratistas quieren producir ellos mismos sus propios requisitos de concreto con una planta mezcladora más pequeña. La atención se centra en los bajos costos de adquisición.
Además del uso estacionario, los subconjuntos pre-montados y los cimientos de acero hacen que la planta de Liebherr sea ideal para un uso móvil, por ejemplo, en obras de construcción o terrenos arrendados. Es posible trasladar la planta de forma muy sencilla, afirma la empresa.
La operación se facilita al operador mediante el uso de un sistema de control intuitivo a través de una computadora portátil.
La transportabilidad y modularidad son características buscadas en nombre de la flexibilidad. Con ese fin, el contratista con sede en Rusia Zentrodostroy decidió invertir en una planta mezcladora de asfalto transportable de Benninghoven.
“Con el TBA 4000, buscamos armarnos para enfrentar los desafíos actuales y prepararnos para el futuro al mismo tiempo”, explica Nikolai Konstantinovich, director de la planta de mezcla en Zentrodostroy. “Tenemos planes a largo plazo para nuestra planta de Benninghoven. Un argumento importante a favor de la inversión fue la opción de modernizar los módulos en cualquier momento para mantener el ritmo del estado de la técnica”, agrega Konstantinovich, al describir las ventajas del diseño modular de la línea TBA.
Específicamente, Zentrodostroy ya tiene sus ojos puestos en la tecnología de alimentación multivariable de Benninghoven. El sistema de alimentación en frío RAP alcanza tasas de material RAP de hasta un 40%, lo que hace que la producción de asfalto sea más rentable y sostenible.
En lugar de deshacerse del asfalto viejo, el sistema de alimentación RAP de Benninghoven lo convierte en una valiosa materia prima. Primero, el material molido elimina por completo el costo del nuevo mineral blanco, y segundo, se requiere menos bitumen para procesarlo en una nueva mezcla en el TBA 4000.
Seguridad ante todo
Una planta mezcladora segura, es productiva. “Trabajamos constantemente para que nuestras plantas sean más seguras”, afirma Tesch, de Ammann. “Esto se refiere a la seguridad laboral pero también a la seguridad operativa. Hoy ya cumplimos con los más altos estándares internacionales.
“El sistema de control juega un papel importante, ya que monitorea todo el proceso, incluidos los límites de emisión y el acceso a los componentes críticos de la planta”, continúa. “Ammann concede gran importancia a la seguridad y la ergonomía para el personal de mantenimiento, por ejemplo, mediante una buena accesibilidad a los componentes de la planta, sistemas de enclavamiento, puertas de servicio y mantenimiento de generosas dimensiones, etc.
“La infraestructura y el sector de construcción de carreteras continuarán desempeñando un papel clave en la economía en el futuro”, señala. “Somos cautelosamente optimistas sobre los desarrollos en los próximos años”, concluye.
CONTÁCTESE CON EL EQUIPO
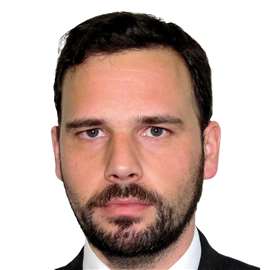