Túnel minero
05 October 2011
Una de las máquinas tuneladoras más grandes de América del Sur, aplicada en minería, se encuentra trabajando en Chile. Se trata del Proyecto Construcción Túnel Sur - Los Bronces, que nace como una necesidad de la empresa minera Anglo American, de contar con un acceso permanente para sondear el futuro Yacimiento Sulfatos. Para lograrlo, "se decidió aplicar una tecnología de punta que presentaba las mejores condiciones de seguridad y plazos de ejecución, mediante la excavación mecanizada utilizando una "máquina tuneladora" o Tunnel Boring Machine, conocida como TBM", comenta Vicente Irarrázaval, vicepresidente de exploraciones de Anglo American.
"En la actualidad con esta misma tecnología se están construyendo túneles en México (8,7 m diámetro), Venezuela (5,85 m diámetro), Panamá (9,73 m diámetro), Ecuador (9 m diámetro), entre otros países latinoamericanos, pero siempre aplicada a obras civiles, mientras que la TBM del Túnel Sur es de las mayores tuneladoras trabajando para la minería en América del Sur", indica.
La construcción del túnel significará un acceso permanente y seguro para la evaluación del proyecto Sulfatos, evitando los inconvenientes climáticos propios de la alta cordillera. El túnel tiene 8.125 m de longitud, y se construye desde un portal ubicado a 3.608 metros sobre el nivel del mar. Se ejecuta en un sólo frente, por lo que se trata de un túnel ciego que no sale a la superficie.
¿Los costos de aplicar la tecnología? "Dependen de la longitud del túnel a excavar, siendo aproximadamente de US$8.500/ml (metros lineales) para túneles del orden de 12 kilómetros y de US$10.000/ml en túneles de ocho kilómetros", señala el ejecutivo.
La tecnología
El equipo cuenta con una tecnología de doble escudo universal, con un diámetro de 4,5 m y 90 m de longitud. Está conformado por tres sectores: 1. Cabeza de Corte, Escudo Delantero y Escudo Telescópico. 2. Escudo de Grippers y Erector de Dovelas y 3. El back up, compuesto por siete carros ferroviarios donde se encuentran instalados los equipos que hacen posible su funcionamiento. Si bien estos segmentos conforman la TBM como un todo, cuando la tuneladora avanza, no lo hacen las tres partes en forma simultánea, quedando postergado el avance del Escudo de Grippers y Erector de Dovelas para una secuencia posterior del ciclo.
La TBM excava a través de la generación de círculos concéntricos en el frente del túnel, producidos por la penetración en la roca de los 28 cortadores de la cabeza de corte, la que a su vez es empujada por ocho cilindros de empuje principales (hidráulicos) generando contra el frente un empuje total de 8.700 kN (kilo newton). De manera de generar la "reacción" necesaria para esta fuerza, la tuneladora se "ancla" lateralmente al túnel ya excavado, a través de dos zapatas o grippers.
La penetración de los cortadores va generando "surcos" en la roca, cada vez más profundos, a medida que impulsan los cilindros de empuje principal, hasta que se genera la rotura de la roca entre dos "surcos" consecutivos, desprendiendo una lámina llamada chip. Cada cortador tiene potencia para cortar cinco toneladas. Los chips son capturados por cuatro tolvas o palas que tiene la cabeza de corte cuando gira en sentido de los punteros del reloj, y son vaciados en un buzón que los traspasa a la cinta transportadora de la tuneladora.
En el carro N°7, el material que circula en la cinta TBM es traspasado a otra cinta anclada al túnel ya terminado, encargada de llevar el material hacia la superficie, material que es almacenado en un acopio a la salida del portal. La máxima potencia del sistema se genera cuando la TBM está excavando y avanzan los cilindros de empuje principales, por lo que es durante esta operación cuando los sectores 1 y 3 se desplazan a la velocidad de penetración de dichos cilindros..
Cada ciclo de excavación es de 1,40 m, una vez terminado, se recogen los grippers y cilindros de empuje principales, quedando listos para iniciar un nuevo ciclo de excavación. A esta operación se le conoce como regripping y es durante ésta cuando el sector 2 avanza los 1,40 m excavados. Por diseño la TBM puede instalar la fortificación, pernos y malla, en paralelo con la excavación, ganando tiempo en el ciclo global, y la fortificación se hace precisamente en el sector 2.
Para desplazarla, la máquina se soporta dependiendo del sector. "El sector 1 se soporta directamente sobre la roca excavada; el sector 2 en forma independiente sobre la estructura de la TBM en el área del sector 1 y el sector 3 sobre rieles de acero, en que se apoyan y fijan a dovelas de piso, elementos prefabricados de hormigón armado", detalla Irarrázabal.
Asimismo, en cada sector de la máquina hay personal especializado. En el erector de dovelas trabajan seis operarios; tres instalando las dovelas de piso y tres en fortificación; en el back up trabajan 12 personas, entre las cuales se encuentran el operador de la TBM, el maestro mecánico y electrónico de la máquina y personal de apoyo, como eléctricos, mecánicos, soldadores, supervisores, encargados del ingreso de materiales y de prolongar la cinta transportadora.
Faenas en el túnel
De fabricación italiana, su diseño y ensamblaje se efectuó en Chile. El fabricante SELI, armó la TBM en sus talleres cercanos a Roma y conectó las principales piezas, de manera de hacer un chequeo completo, lo que mejoraba la respuesta ante la ocurrencia de una falla grave de operatividad que se detectara durante las pruebas.
Tras ser recibida en Roma por el mandante, fue desarmada y enviada a Chile vía marítima, dispuesta en más de 90 bultos. A su llegada a Chile, se trasladaron desde el puerto de Valparaíso hasta la División Los Bronces y de ahí al portal del túnel, ubicado a 3.608 m de altura, con temperaturas de hasta -25°C, caminos cortados por la nieve y un acceso estrecho y desalineado respecto a su eje.
El portal de acceso al túnel se construyó en la ladera de un cerro, por lo que no existía espacio suficiente para hacer el montaje del equipo en el exterior, lo que habitualmente sucede en proyectos parecidos, siendo necesario iniciar las excavaciones con el método Drill & Blast y construir una caverna subterránea, de 8,60 x 6,80 x 95 m, para ensamblar finalmente la máquina, y desde ese punto continuar el túnel aplicando la TBM. Desde el inicio, hasta los 500 metros, hubo que sortear una roca fracturada o diaclasada. Para solucionarlo, el consorcio constructor a cargo del proyecto, Dragados-Besalco, aplicó hormigón proyectado y dovelas metálicas. Después de los 500 metros, la fortificación se ejecutó en base a pernos y malla Acma, que dejan la superficie del túnel expuesta. Ante la mala calidad del terreno se terminó por avanzar con excavadora y martillo picador, para evitar posibles derrumbes del techo del túnel. Fueron 185 metros excavados en base a perforación tradicional en conjunto con equipamiento manual.
Otro reto. La aplicación de la TBM es una tecnología nueva en el país, de hecho, este proyecto es el segundo que se aplica en túneles mineros. La primera experiencia con TBM se desarrolló en el túnel acueducto Río Blanco, en el Teniente, en 1993. Se excavó un túnel de 4,6 metros de diámetro y 11 km de largo y fue excavado mediante tuneladora en una longitud de 10 km y 1 km con método tradicional.
Ante la escasa experiencia, "no existían especialistas en su operación, mantención y reparación. Por ello, dentro del alcance de la compra de la TBM, se incluyó que la operación, mantenimiento y reparación estuviera a cargo del fabricante SELI", detalla Irarrázabal.
Desarme TBM
La TBM ha alcanzado un rendimiento promedio de avance en los últimos meses cercano a los 22 m por día, en que el récord fue de 36,9 m diarios (no obstante, el domingo 23 de enero de 2011, se logró excavar 46,1 metros en el día) y, a la fecha "llevamos 6.243 metros de los 7.917 metros contemplados", confirma el ejecutivo.
Una vez concluya la construcción del túnel, el próximo reto será el desarme y retiro de la TBM. "Se están estudiando varias alternativas respecto al desarme, que está contemplado comenzar en diciembre de 2011. Es un desafío técnico ya que se trata de un túnel pequeño y se debe desmovilizar la TBM en retroceso, pasar por sectores con sostenimiento de marcos de acero, ductos metálicos de ventilación, refugios y cinta transportadora. Sacar el back-up no es tan complicado, ya que son carros independientes que pueden ser remolcados por la vía férrea; en cambio, de la TBM hay que desacoplar la cabeza, escudos, motores, cilindros, cuyo manejo, tanto en volumen como en peso, requieren de instalaciones adicionales", comenta el ejecutivo de Anglo American.
Por ello es que su diseño consideró que la cabeza de corte se conformara de dos partes, las cuales son "colapsables", lo que permitirá su retiro una vez que la máquina se desarme, faena que estará a cargo del fabricante. Un desarrollo pionero para la construcción de túneles en Chile.
CONTÁCTESE CON EL EQUIPO
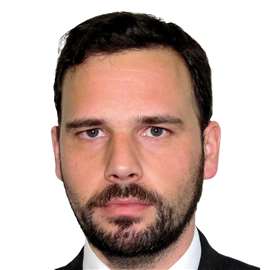